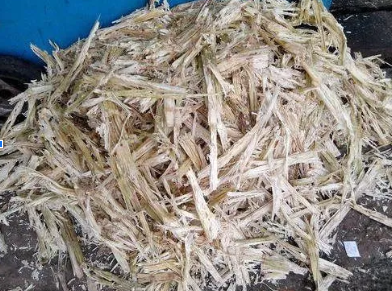
Key Questions Answered in this Section
- What is sugarcane bagasse, and how is it generated as a byproduct of sugarcane processing?
- How much bagasse is produced annually in India, and which states generate the most?
- What are the key characteristics of sugarcane bagasse in loose and briquette forms?
- How is bagasse utilized in cogeneration for heat and electricity in the sugar industry?
- What are the primary industrial applications of bagasse beyond power generation?
- How is bagasse processed into forms like briquettes and pellets for efficient use?
- Which industries in India rely on bagasse for heating and energy needs?
- What types of boilers are suitable for burning bagasse in industrial settings?
- What are the challenges in storing, transporting, and using bagasse as biomass fuel?
- How does the use of bagasse compare to fossil fuels in terms of cost, efficiency, and environmental impact?
- How is the price of sugarcane bagasse in loose form determined, and what factors influence the cost in India?
- How is the price of sugarcane bagasse in briquette form determined, and what factors influence the cost?
- Is it possible to directly use bagasse in boilers?
Introduction
Sugarcane bagasse is the fibrous residue left after extracting juice from sugarcane stalks, comprising roughly 40-50% cellulose, 25-30% hemicellulose, and 20-25% lignin. Produced in large volumes—about 280 kg of bagasse per ton of sugarcane—this byproduct is a valuable biomass resource.
It’s primarily used as a raw material for generating bioenergy through direct combustion for steam and electricity in sugar mills, as well as for producing second-generation bioethanol via enzymatic hydrolysis. Additionally, bagasse serves as a feedstock for bioplastics, paper production, and biochar, making it a versatile and sustainable alternative to fossil fuels and synthetic materials.
Expert Consulting Assistance for Indian Bioenergy & Biomaterials
Talk to BioBiz
Call Muthu – 9952910083
Email – ask@biobiz.in
Let us look into the price, availability, and proximate analysis of bagasse briquettes and pellets, their use in boilers, and the role of transport and logistics in their efficient distribution.
Total Bagasse Generation in India
Annual Generation: India generates approximately 105 million tonnes of bagasse annually from sugar mills. Assessing the availability of bagasse involves analyzing its proximate analysis to determine suitability for various applications.
Biomass Characteristics
The table summarizes proximate analysis (moisture, volatile matter, ash, fixed carbon) and feedstock costs, highlighting quality and economic feasibility. The proximate analysis of bagasse reveals its efficiency when used in boilers, highlighting its potential as a renewable energy source.
Parameter | Loose Form | Briquette Form |
Gross Calorific Value (GCV) | —— | 3700 Kcal/kg |
Moisture Content | 50% | 12-15% |
Ash Content | 3% | 3% |
Silica Content | 5-8% | 5-8% |
Volatile Matter | 85% | 80% |
Fixed Carbon | 12% | 20% |
Bulk Density | 200-250 Kg/m3 | 750-800 Kg/m3 |
Price | ₹2 to ₹3.5 per kg | ₹6.5 per kg |
Seasonality
- Tamil Nadu: Main season (December-May) with early (Dec-Jan), mid (Feb-Mar), and late (Apr-May) crops. A special season (June-July) is also practiced, especially in certain districts.
- Karnataka: Planting occurs in Dec-Feb (Eksali, 12-month crop), Oct-Nov (Preseasonal, 15-16 month crop), and July-Aug (Adsali, 18-month crop).
- Kerala: Normal planting occurs from October to December. Planting should not be delayed beyond February in plains and post-heavy rains in hilly regions.
Season | Tamil Nadu | Karnataka | Kerala |
December to January | ✅ (Early crop) | ✅ (Eksali, 12-month crop) | ✅ (Normal planting season) |
February to March | ✅ (Mid crop) | ✅(Eksali, 12-month crop) | ✅ (Should not delay beyond February) |
April to May | ✅ (Late crop) | ✅(Eksali, 12-month crop) | ❌ |
June to July | ✅(Special season) | ❌ | ❌ |
July to August | ❌ | ✅(Adsali, 18-month crop) | ❌ |
October to November | ✅ | ✅(Preseasonal, 15-16 month crop) | ✅(Normal planting season) |
October to December | ✅ | ✅(Preseasonal, 15-16 month crop) | ✅ (Post-heavy rains in hilly regions) |
Regional Availability
Regions with abundant bagasse availability can leverage this resource for use in boilers, promoting sustainable energy practices. The following are the top five states in India where sugarcane is abundantly available, along with key regions within those states:
State | Annual Sugarcane Production (MTPA) | Annual Bagasse Generation (MTPA) | Key Regions of State |
Uttar Pradesh | 177 | 49.5 | Meerut, Bareilly, Saharanpur, Bulandshahr |
Maharashtra | 110 | 31 | Pune, Satara, Solapur, Ahmednagar, Aurangabad |
Karnataka | 61 | 17 | Shimoga, Mysuru, Belgaum, Chitradurga |
Gujarat | 17 | 4.75 | Valsad, Navsari, Surat, Bharuch |
Tamil Nadu | 15 | 4 | Coimbatore, Erode, Tiruppur, Trichy, Madurai, Theni, Tirunelveli |
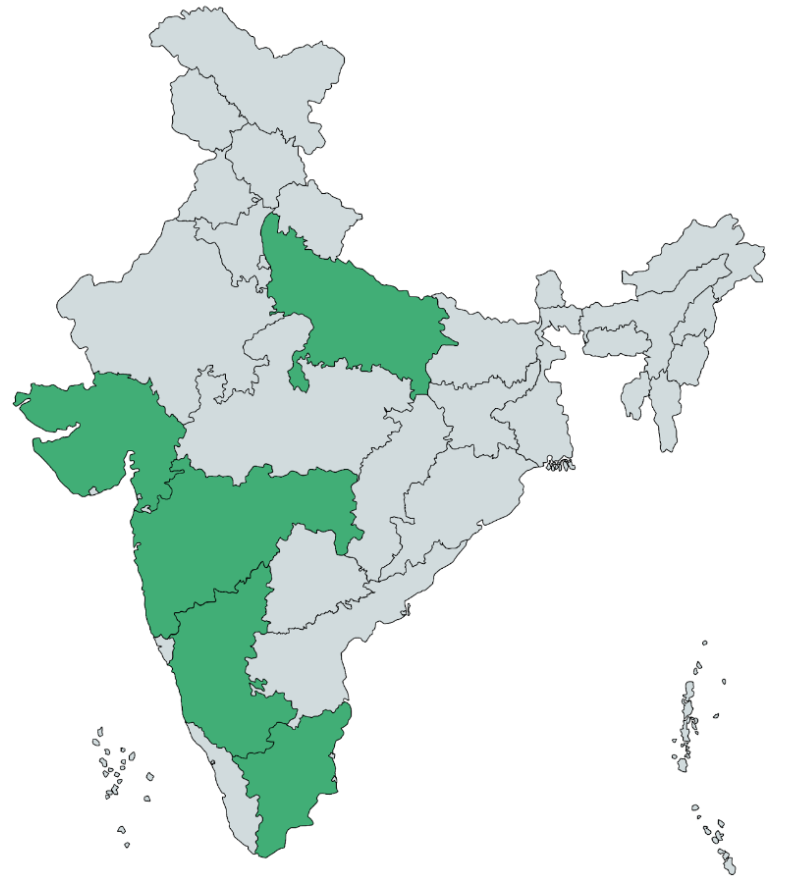
Prices
- The price of raw bagasse varies based on region, supply, and demand dynamics.
- Raw Bagasse: ₹2 to ₹3.5 per kg.
- Bagasse Briquettes: ₹6.5 per kg
- Fluctuations in bagasse price directly impact the cost-effectiveness of producing briquettes and pellets for industrial boiler use.
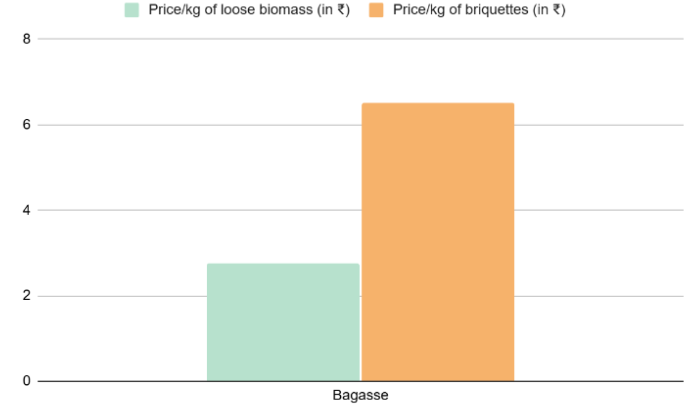
Uses of Bagasse
Current Uses
- Captive power generation: Bagasse is used within sugar mills to produce power, reducing the need for external energy sources.
- Paper and pulp industry: A major alternative use of bagasse is in the production of paper.
Emerging Uses
- Building Materials: Bagasse fibres are used in construction materials, offering lightweight and sustainable options.
- Ethanol Production: Bagasse serves as a feedstock for cellulosic ethanol, reducing reliance on fossil fuels.
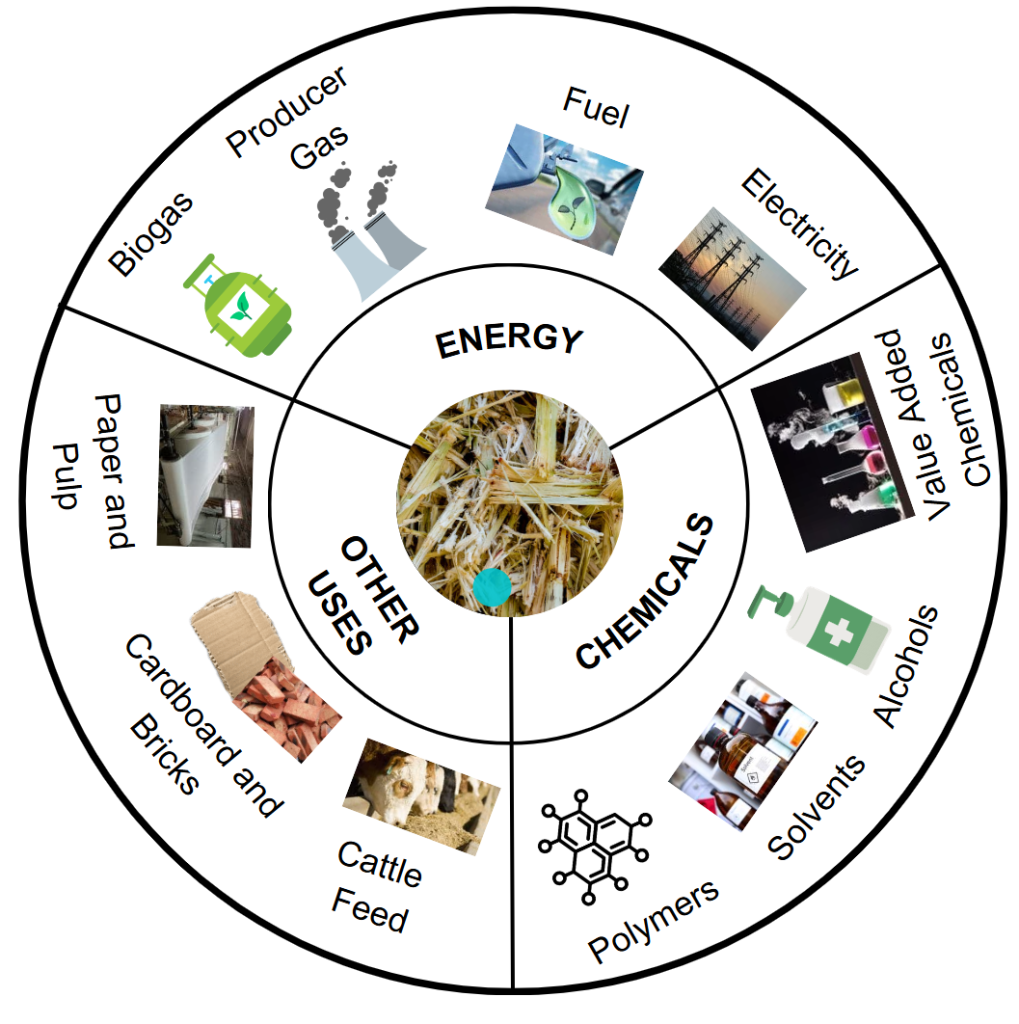
Storage of Bagasse
- Moisture content: Bagasse typically has a moisture content of 45-50%. It needs to be stored in a dry condition to prevent degradation and loss of calorific value.
- Storage methods: Open-air storage is common, but it poses risks of moisture absorption and fungal growth. Covered sheds or silos are recommended to protect bagasse from rain and reduce moisture reabsorption.
- Seasonality: Since bagasse is produced during the sugarcane crushing season (October to March), large quantities need to be stored for off-season usage. This makes efficient storage crucial.
- Self-ignition risk: Bagasse is prone to self-combustion due to its high cellulose content. It should be stored in controlled environments, avoiding stacking heights greater than 10-12 meters to reduce fire hazards.
- Utilization: About 90% of bagasse in India is used by sugar mills for captive power generation, while 10% is used for paper and ethanol production.
- Proper storage ensures that bagasse briquettes and pellets maintain their quality, facilitating efficient transport and logistics to various regions.
Bagasse as Feedstock – Key Challenges
- Seasonal Availability: Bagasse is a by-product of sugarcane processing, making it available mainly during the sugarcane crushing season (October to March), limiting its year-round utility. This leads to challenges in maintaining continuous supply for power generation and industrial use.
- Storage Issues: Bagasse has high moisture content (up to 50%) and is bulky, leading to difficulties in transportation and long-term storage. Poor storage facilities often result in spoilage due to microbial activity or fires, reducing its energy potential.
- Logistical Constraints: Transporting bagasse from sugar mills to power plants or industries increases operational costs. Sugar mills are often located in rural areas with underdeveloped infrastructure, causing additional challenges in logistics.
- Low Energy Density: Bagasse has a lower energy density compared to other biomass feedstocks, with a calorific value of 1,800-2,000 kcal/kg. This necessitates larger volumes to produce equivalent energy, reducing efficiency in biomass energy projects.
- Competing Uses: Bagasse is used for multiple purposes, such as paper production, bioenergy, and cattle feed. These competing industries drive up demand and limit availability for specific applications like biofuel production.
- Technological Limitations: Efficient conversion of bagasse to biofuels, bioethanol, or energy requires advanced technology, which remains underdeveloped in India. Conventional cogeneration plants face efficiency challenges, with many plants still operating below 30% efficiency.
Bagasse for Industrial Heating and Power Generation in India
Uses of Bagasse for Industrial Heating and Power Generation
Bagasse has found substantial utility in industries for generating both heat and power, thanks to its high calorific value. In India’s sugar industry, which produces around 400-450 million tonnes of sugarcane annually, approximately 30% of the sugarcane mass turns into bagasse. Here’s how bagasse is utilized:
- Cogeneration of Heat and Electricity: Bagasse is primarily used for cogeneration in sugar mills, producing both electricity and steam. In a cogeneration setup, bagasse combustion generates steam at high pressures, driving turbines to produce electricity while simultaneously supplying steam for industrial heating. Over 90% of India’s sugar mills have cogeneration plants, significantly reducing reliance on grid electricity.
- Industrial Heating: Industries like paper, cement, and textiles have adopted bagasse for their heat requirements. The steam generated during bagasse combustion is directly used for drying, cooking, and other thermal processes, decreasing the use of fossil fuels.
- Bioethanol Production: While primarily used for heat and power, bagasse’s potential extends to second-generation bioethanol production, which India is investing in as part of its National Biofuel Policy.
Forms in Which Bagasse is Used in Industries
The form in which bagasse is used varies depending on the industry and the purpose:
- Raw Bagasse: Freshly obtained from sugar mills, raw bagasse is generally used without any further processing in cogeneration plants within the sugar industry. It retains 45-50% moisture, making it suitable for large boilers that can handle high-moisture content fuel.
- Dried Bagasse: To increase energy efficiency, some industries use dried bagasse, which has a lower moisture content (around 10-15%). Drying improves its calorific value, leading to better combustion efficiency.
- Pelletized or Briquetted Bagasse: For industries requiring standardized fuel, bagasse is sometimes compacted into pellets or briquettes. This form is easier to transport and store and has higher energy density, making it a preferred choice in smaller industrial settings that rely on biomass.
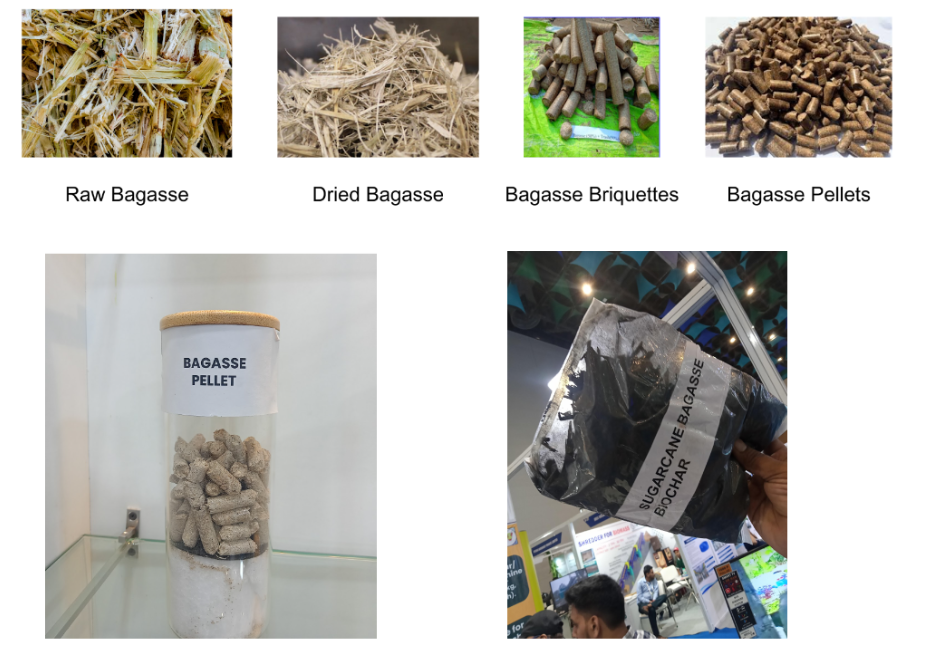
The figures above displays bagasse pellets and bagasse biochar observed at the India Bioenergy & Tech Expo held in September 2024.
Boilers Using Bagasse
Boilers are crucial to harnessing the energy in bagasse. They are specially designed to handle its unique properties, like high moisture and fibrous content. Here are some types of boilers commonly used in India:
- Travelling Grate Boilers: These boilers are ideal for burning biomass fuels like bagasse. They have a moving grate that allows bagasse to burn efficiently as it travels through the combustion chamber. Travelling grate boilers are popular in Indian sugar mills due to their robust design and ease of handling wet bagasse.
- Fluidized Bed Boilers: These advanced boilers use a bed of solid particles that circulate inside the combustion chamber, ensuring uniform temperature and efficient combustion. Fluidized bed boilers are gaining popularity in India for industrial heating because of their higher efficiency and ability to handle various biomass types, including bagasse.
- Pneumatic Spreader Stoker Boilers: These boilers use air to distribute bagasse evenly over the combustion grate, ensuring better fuel-air mixing and efficient combustion. They’re common in plants with varying bagasse moisture levels, as the pneumatic system helps optimize the burn.
Amount of Bagasse Being Used by the Industries for Industrial Heating
India’s sugar industry alone generates over 100 million tonnes of bagasse annually, a majority of which is utilized for industrial heating and power generation. Here are some relevant data points on bagasse usage:
- Sugar Industry: Indian sugar mills consume about 70-75% of bagasse they produce for captive power generation and steam production. An average-sized sugar mill with a 5,000-tonne daily crushing capacity (TCD) generates about 6.5-7 MW of electricity using bagasse during the crushing season.
- Cogeneration Capacity: India’s sugar industry boasts an installed cogeneration capacity of approximately 7,500 MW, driven mainly by bagasse. This figure represents about 13-14% of the total biomass-based power generation capacity in India.
- Export to the Grid: In states like Maharashtra and Uttar Pradesh, surplus electricity from cogeneration plants is exported to the state grid. Approximately 2,000-3,000 MW of power generated from bagasse cogeneration is sold to utilities annually.
Prominent Industries Using Bagasse for Industrial Heating
The use of bagasse extends beyond sugar mills to various industries that are increasingly adopting biomass-based heating systems. Some of the major sectors in India utilizing bagasse include:
- Paper and Pulp Industry: Bagasse is a primary raw material for paper manufacturing, with several paper mills using bagasse-based boilers to generate steam and electricity. Mills like Tamil Nadu Newsprint and Papers Limited (TNPL) heavily rely on bagasse, saving costs and reducing emissions compared to wood pulp.
- Distilleries: Indian distilleries, especially those located near sugar mills, use bagasse as a fuel source for distillation processes, driving boilers that generate the necessary steam.
- Food Processing: The food processing industry utilizes bagasse in its boilers to power drying and cooking processes, offering a cleaner alternative to coal or diesel. Bagasse-fired boilers are common in Maharashtra’s sugar belts, where they support local food processing facilities.
- Cement Industry: Cement plants in India are starting to adopt biomass, including bagasse, as an alternative fuel for kiln heating. While still in its nascent stage, this transition is driven by the need to lower carbon footprints.
Expert Consulting Assistance for Indian Bioenergy & Biomaterials
Talk to BioBiz
Call Muthu – 9952910083
Email – ask@biobiz.in