Key Questions Answered in this Section
- What are cotton stalks, and why are they considered a valuable biomass feedstock?
- How much cotton stalk biomass is generated annually in India, and what are its primary uses?
- What are the key characteristics of cotton stalks in loose and briquette forms?
- Why are cotton stalks a sustainable alternative for industrial heating and power generation?
- How are cotton stalks processed into briquettes, pellets, and other industrial-use forms?
- What are the main challenges in collecting, storing, and transporting cotton stalk biomass?
- Which states in India produce the most cotton stalks, and what are the key regions?
- How do industries like textiles, sugar mills, and food processing utilize cotton stalk biomass?
- What types of boilers are suitable for burning cotton stalks in industrial applications?
- How does the use of cotton stalk biomass compare to coal in terms of energy output and cost savings?
- How is the price of cotton stalk biomass in loose form determined, and what factors influence the cost in India?
- How is the price of cotton stalk biomass in briquette form determined, and what factors influence its cost?
- Is it possible to directly use cotton stalks in boilers?
Introduction
Cotton Stalks Biomass Feedstock: Cotton stalks are the lignocellulosic residues left behind after the cotton lint has been harvested. These residues consist of the main stems, branches, and leaves, typically ranging from 0.5 to 1.5 meters in height.
Expert Consulting Assistance for Indian Bioenergy & Biomaterials
Talk to BioBiz
Call Muthu – 9952910083
Email – ask@biobiz.in
The stalks are rich in cellulose (around 40-50%), hemicellulose (20-30%), and lignin (15-25%), which makes them suitable for multiple biomass applications.
The high cellulose content allows for efficient conversion into biofuels, such as bioethanol and biodiesel, while the lignin can be used for biochar production. Cotton stalks can also be converted into pellets or briquettes for use as solid biofuel in combustion processes, and they are a promising feedstock for biogas production via anaerobic digestion.
Let us look into the price, availability, and proximate analysis of cotton stalk briquettes and pellets, their use in boilers, and the role of transport and logistics in their efficient distribution.
Total Cotton Stalk Generation in India
- The total generation of cotton stalk in India is estimated at around 20 million tonnes per annum (at 10% moisture content).
- Assessing the availability of cotton stalk involves analyzing its proximate analysis to determine suitability for various applications.
Biomass Characteristics
The table summarizes proximate analysis (moisture, volatile matter, ash, fixed carbon) and feedstock costs, highlighting quality and economic feasibility. The proximate analysis of cotton stalk reveals its efficiency when used in boilers, highlighting its potential as a renewable energy source.
Parameter | Loose Form | Briquette Form |
Gross Calorific Value (GCV) | NA | 3800 kcal/kg |
Moisture Content | 15% | 10% |
Ash Content | 7% | 10% |
Silica Content | 2-5% | NA |
Volatile Matter | 80% | 77% |
Fixed Carbon | 13% | 13% |
Bulk Density | 225 Kg/m3 | 630 Kg/m3 |
Price | ₹3-3.5/Kg | ₹7/Kg |
Seasonality
Cotton is predominantly a kharif crop, with sowing varying based on regional climatic conditions:
- Northern India (Punjab, Haryana, Rajasthan):
- Cotton sowing begins early, around April-May, in irrigated areas.
- Central India (Madhya Pradesh, Maharashtra, Gujarat):
- Irrigated cotton is sown from March-May, while rainfed cotton is planted in June-July with the onset of the monsoon.
- Southern India (Andhra Pradesh, Telangana, Karnataka, Tamil Nadu):
- In Tamil Nadu, irrigated and rainfed crops are mostly sown between September-October, with rainfed sowing extending up to November in some districts. In some parts of Karnataka and Andhra Pradesh, desi cotton is sown during August-September. Additionally, summer sowings in Tamil Nadu occur in February-March.
- Rice fallows of Andhra Pradesh and Tamil Nadu:
- Cotton sowing happens from mid-December to mid-January.
State | April-May (Irrigated) | March-May (Irrigated) | June-July (Rainfed) | September- October (Irrigated) | August-September (Desi cotton) | February-March (Summer) | Mid-December to Mid-January |
Punjab | ✅ | ❌ | ❌ | ❌ | ❌ | ❌ | ❌ |
Haryana | ✅ | ❌ | ❌ | ❌ | ❌ | ❌ | ❌ |
Rajasthan | ✅ | ❌ | ❌ | ❌ | ❌ | ❌ | ❌ |
Madhya Pradesh | ❌ | ❌ | ✅ | ❌ | ❌ | ❌ | ❌ |
Maharashtra | ❌ | ✅ | ✅ | ❌ | ❌ | ❌ | ❌ |
Gujarat | ❌ | ✅ | ✅ | ❌ | ❌ | ❌ | ❌ |
Andhra Pradesh | ❌ | ❌ | ❌ | ✅ | ✅ | ❌ | ✅ |
Telangana | ❌ | ❌ | ❌ | ✅ | ✅ | ❌ | ❌ |
Karnataka | ❌ | ❌ | ❌ | ✅ | ✅ | ❌ | ❌ |
Tamil Nadu | ❌ | ❌ | ❌ | ✅ | ✅ | ✅ | ✅ |
Regional Availability
Regions with abundant cotton stalk availability can leverage this resource for use in boilers, promoting sustainable energy practices. The following are the top 5 states in cotton cultivation.
State | Total Crop Production (MTPA) | Key Regions of State |
Gujarat | 7.5 | Amreli, Bhavnagar, Junagadh, Rajkot |
Maharashtra | 7 | Nagpur, Aurangabad, Jalna |
Telangana | 6 | Adilabad, Warangal, Khammam |
Rajasthan | 2.5 | Sri Ganganagar, Hanumangarh, Alwar, Nagaur |
Karnataka | 2 | Bijapur, Dharwad, Bellary |
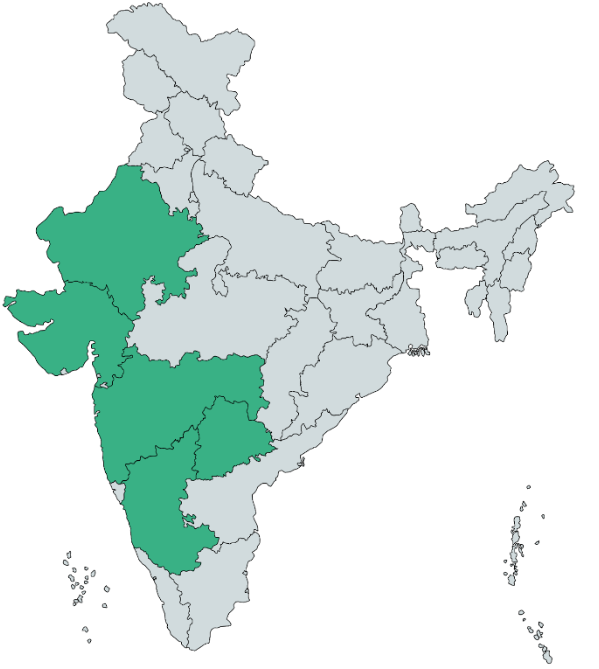
Prices
The price of cotton stalk ranges from ₹3 to ₹3.5 per kg in its raw form, while briquettes made from cotton stalk are priced at around ₹7 per kg. Fluctuations in cotton stalk price directly impact the cost-effectiveness of producing briquettes and pellets for industrial boiler use.
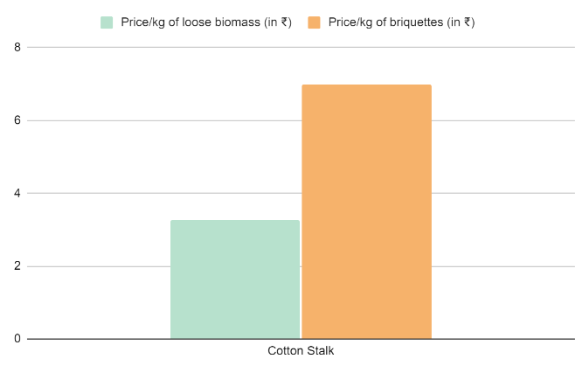
Uses of Cotton Stalks
- Particle Board Production: Used to manufacture particle boards that are cost-effective and meet industrial standards.
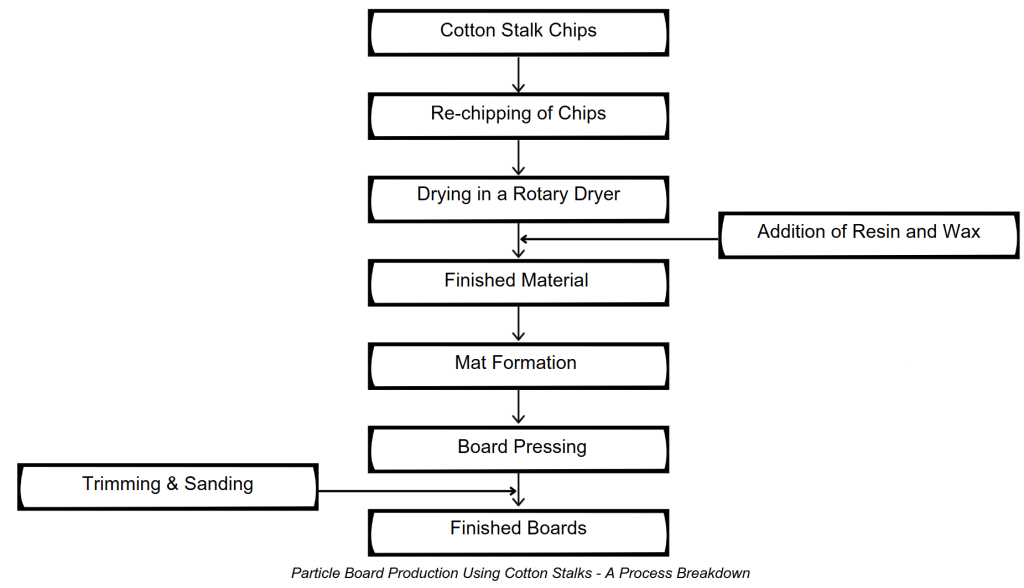
- Animal Feed: Processed into roughage for livestock feed after treatment to improve digestibility.
- Hardboard Manufacturing: Utilised in producing high-strength hardboards through thermo-mechanical pulping.
- Bioethanol Production: Converted into bioethanol through hydrolysis and fermentation, offering a renewable fuel source.
- Biochar Production: Converted into biochar for use as an anode material in lithium-ion batteries, enhancing energy storage solutions.
Storage of Cotton Stalks
- Storage Practices:
- Traditional Storage: Most farmers stack stalks in open areas, leading to 20-30% losses due to moisture, fungal attacks, and degradation.
- Improved Methods: Covered storage using tarpaulin or thatched structures can reduce losses to 10-15%.
- Moisture Content: Ideal storage conditions maintain the stalks’ moisture content below 12% to prevent microbial decay.
- Briquetting and Pelleting: Some cotton stalks are processed into briquettes or pellets, reducing storage space by up to 80% and increasing the shelf life by 6-12 months. Proper storage ensures that cotton stalk briquettes and pellets maintain their quality, facilitating efficient transport and logistics to various regions.
Cotton Stalk as Feedstock – Key Challenges
- Collection and Transportation: Cotton stalks are scattered across vast fields, making collection inefficient. Transportation costs are high due to low bulk density, which leads to expensive logistics.
- Storage Issues:
- Cotton stalks are highly susceptible to degradation from moisture and pests, especially during monsoon seasons, which results in losses of up to 25% in some cases.
- Space: Farmers often lack adequate storage facilities, leading to wastage of up to 40% in certain regions.
- Pest Infestation: Improper storage leads to issues like termites, increasing feedstock loss.
- Low Energy Yield: The calorific value of cotton stalks is around 3800 kcal/kg, which is lower than other agricultural residues like rice husk. This makes it less attractive as a bioenergy source.
- Competing Uses: Farmers often use cotton stalks as fuel for domestic purposes or as a cheap alternative for livestock feed, reducing the available supply for industrial applications like bioenergy or pulp production.
- Lack of Awareness and Technology: Many farmers lack knowledge about the commercial value of cotton stalks. Furthermore, there is limited availability of efficient processing technology for converting the stalks into biofuels or other value-added products.
Cotton Stalks for Industrial Heating and Power Generation
Uses of Cotton Stalks for Industrial Heating and Power Generation
Cotton stalks have emerged as a sustainable and cost-effective alternative to conventional fuels like coal and wood. In India, industries are increasingly turning to cotton stalks for several reasons:
- Biomass Energy Source: Cotton stalks are an excellent source of biomass. They have high cellulose content, making them ideal for combustion. They are primarily used to generate heat in industrial boilers, reducing reliance on fossil fuels and lowering greenhouse gas emissions.
- Power Generation: Cotton stalks are also employed in biomass power plants. They are converted into bio-pellets or briquettes, which can be burned to produce electricity. This method not only provides a renewable energy source but also contributes to rural employment and waste management.
- Cost Savings: Cotton stalks are often available at a lower price compared to traditional fuels, providing industries with a significant cost-saving opportunity. This is particularly crucial for small and medium-sized enterprises (SMEs) in India that face fluctuating fuel prices.
Form in Which Cotton Stalk is Used in Industries
To make cotton stalks suitable for industrial use, they are processed into various forms:
- Briquettes: One of the most common forms, briquetting involves compressing cotton stalks into small, dense blocks. These briquettes have a high calorific value, making them suitable for industrial heating applications.
- Pellets: Cotton stalks are also transformed into pellets, which are small, cylindrical particles. Pellets are preferred in industrial settings due to their uniform size and ease of handling. They are often used in industrial boilers for heat generation.
- Chips and Powder: Some industries use cotton stalks in a shredded form or as powder. This form is particularly common in smaller furnaces or customized industrial heating setups.
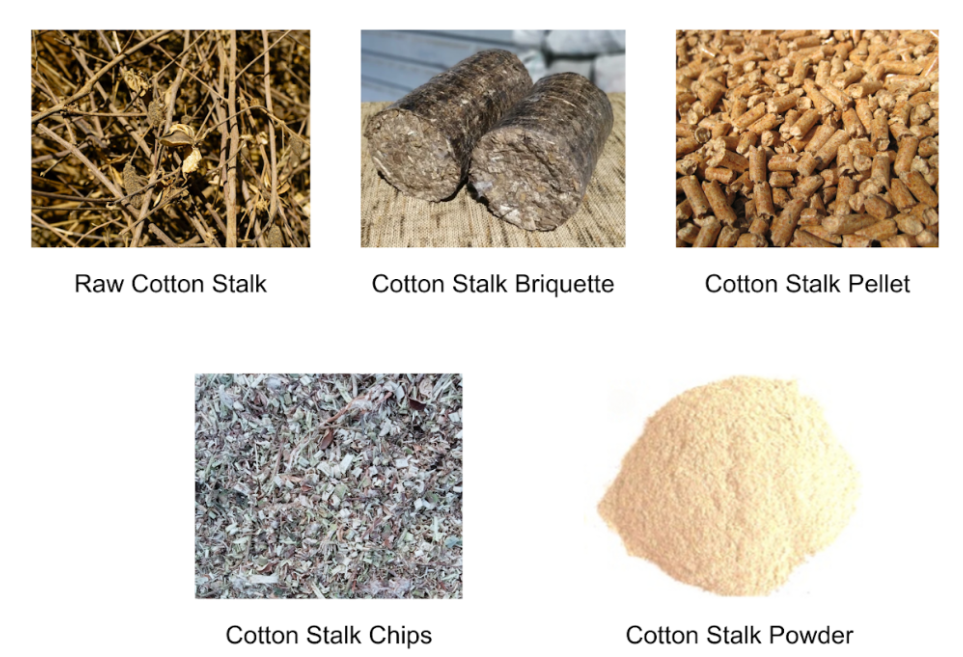
Boilers Using Cotton Stalk in India
Several types of industrial boilers are designed to handle biomass like cotton stalks:
- Fluidized Bed Combustion (FBC) Boilers: These boilers are the most common type used in India for burning biomass. FBC boilers provide efficient combustion of cotton stalks by suspending them in a hot fluidized bed of ash and air, enhancing the thermal efficiency.
- Biomass Stoker Boilers: This type of boiler uses a stoker to feed the biomass fuel (like cotton stalks) into the combustion chamber. These boilers are especially prevalent in smaller industries that require moderate steam generation.
- Water Tube Boilers: Water tube boilers are used in larger installations requiring higher pressure and greater steam capacity. Cotton stalk pellets are a common fuel source for these boilers in the agro-industrial sector.
Amount of Cotton Stalk Being Used by the Industries for Industrial Heating
India produces approximately 20 million tonnes of cotton stalks annually. A significant portion, about 20-25%, is now being utilized by industries for biomass energy production. To put this in perspective:
- 1 tonne of cotton stalks can produce roughly 400-500 kWh of electricity or generate 4,000-5,000 MJ of thermal energy, depending on the efficiency of the boiler and the form of cotton stalk utilized.
- By utilizing this biomass, Indian industries are estimated to save around 5-8% on fuel costs compared to traditional coal.
Prominent Industries Using Cotton Stalk for Industrial Heating
A variety of sectors in India are turning to cotton stalks as a sustainable fuel source:
- Textile and Dyeing: Some textile mills in Gujarat and Maharashtra, the leading cotton-producing states, use cotton stalk biomass for steam generation in dyeing and processing. This has reduced operational costs while enhancing sustainability credentials.
- Sugar Mills: Sugar industries in Tamil Nadu and Karnataka have adopted cotton stalks as a co-fuel in their boilers to manage costs during off-seasons when bagasse availability is low.
- Food Processing Units: Food processing industries, particularly in Andhra Pradesh, are using cotton stalk briquettes for drying and roasting operations. The consistent heat output makes briquettes an attractive option.
- Small and Medium Enterprises (SMEs): Many SMEs in Punjab and Haryana, dealing in agro-processing and metal fabrication, have shifted to cotton stalks to leverage cost benefits and reduce carbon footprints.
Expert Consulting Assistance for Indian Bioenergy & Biomaterials
Talk to BioBiz
Call Muthu – 9952910083
Email – ask@biobiz.in